So the next part of a pump that we are giving an introduction to is mechanical seals. These little components may seem simple but they do a lot of work and make the pump function. I try and break down what a mechanical seal is into simple terms. If you are looking for a new mechanical seal we have a wide range IN STOCK in our webshop.
What Exactly Is a Mechanical Seal?
Inside your water pump, as we have described so far, is an impellor and housing. The impellor is screwed onto a metal shaft that is joined outside the pump to a motor, normally an electric motor. Now when the motor turns on an runs this spins the impellor which creates pressure and flow in the water that is slung through the impellor. Now in a normal centrifugal pump once the water has been pushed through the impellor, it enters the pressurised half of the pump housing. From here it wants to escape though any outlet that is in the housing. This is usually just the outlet pipe, where the pressurised water travels down to be used in the kitchen or bathroom or to water your lawn.
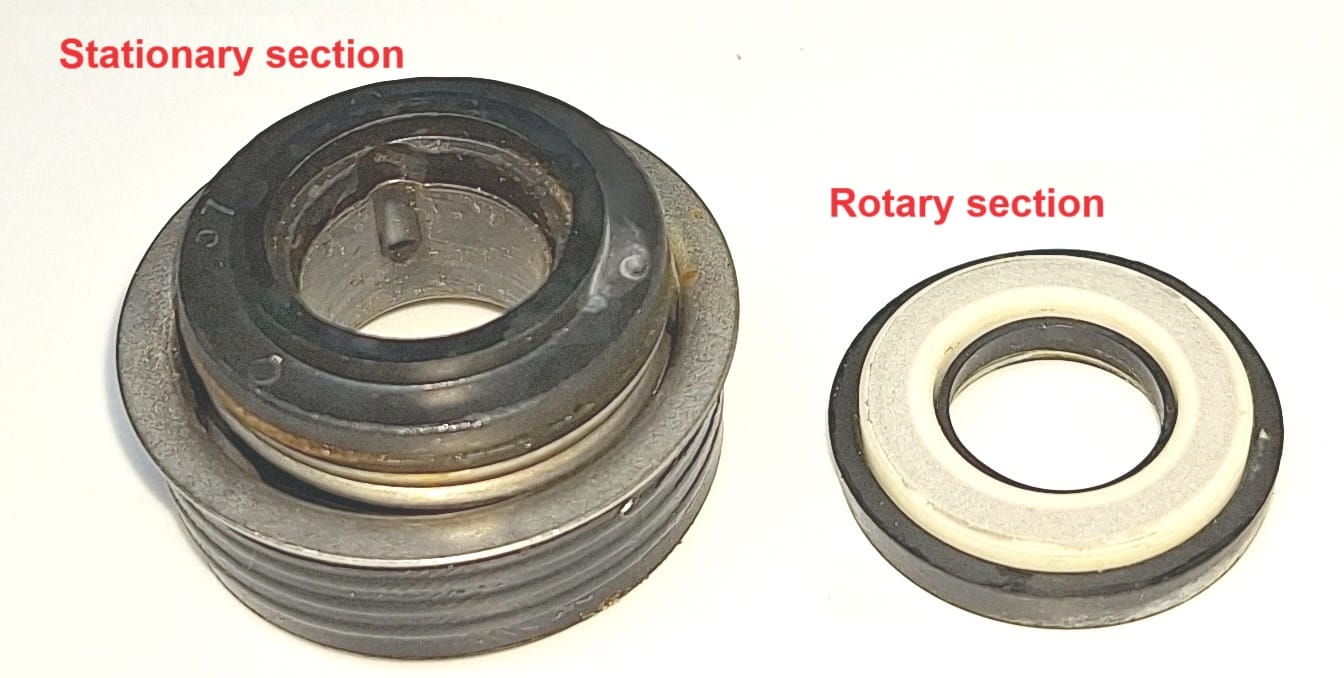
A type 6A mechanical seal with a carbon stationary and ceramic rotary
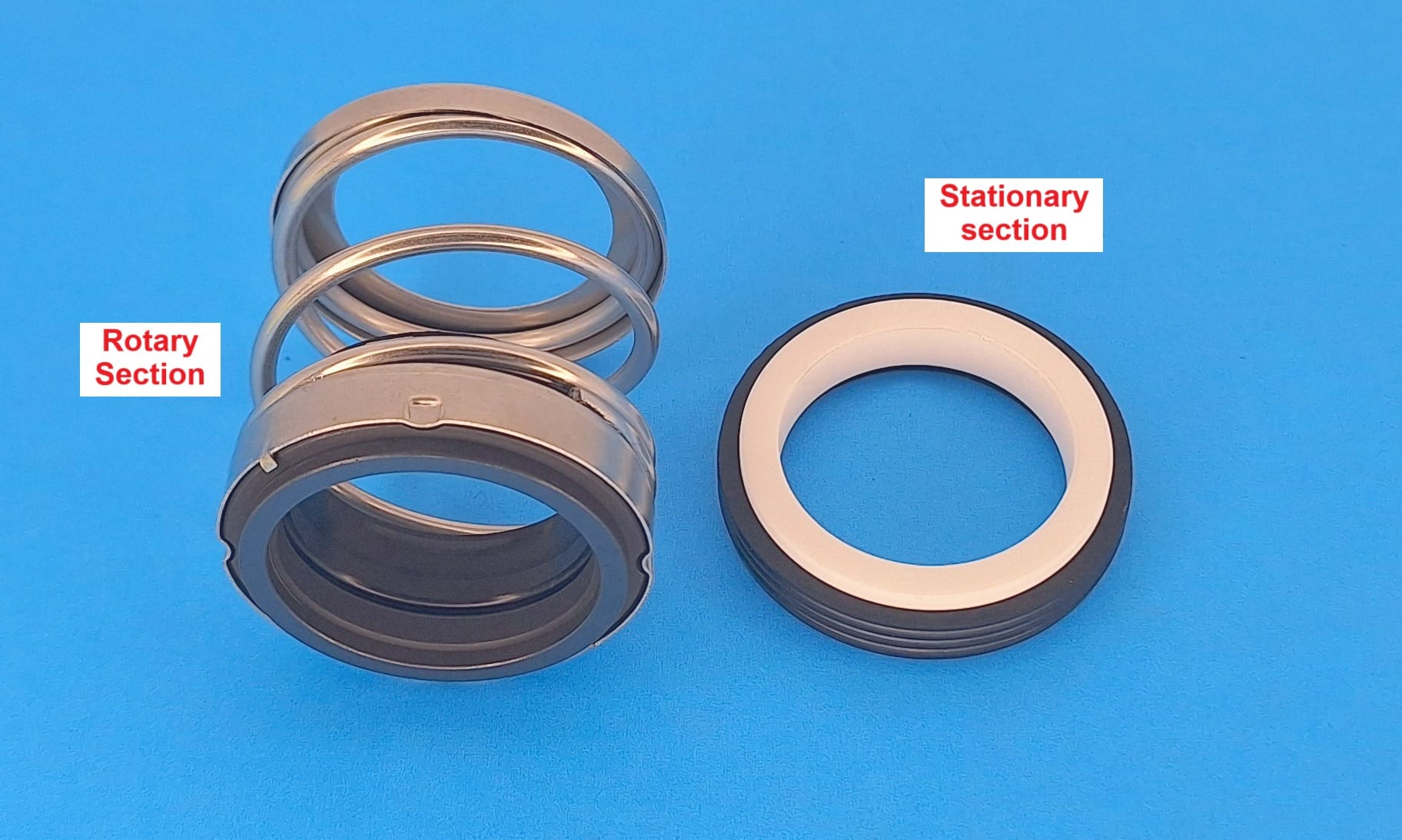
A type 21 mechancial seal with a ceramic stationary and a carbon rotary
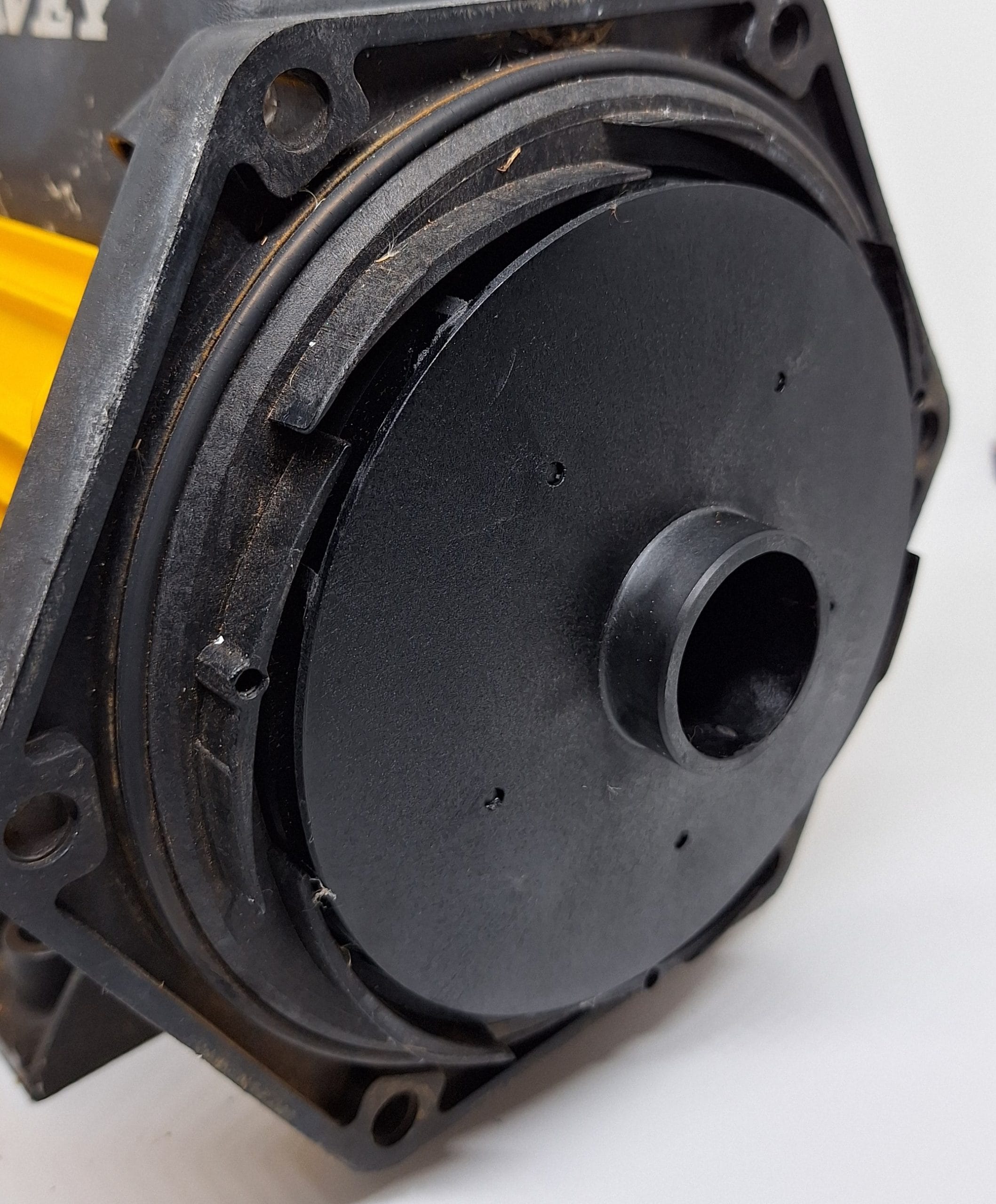
A Davey XJ series pump with the housing removed. This is the impellor.
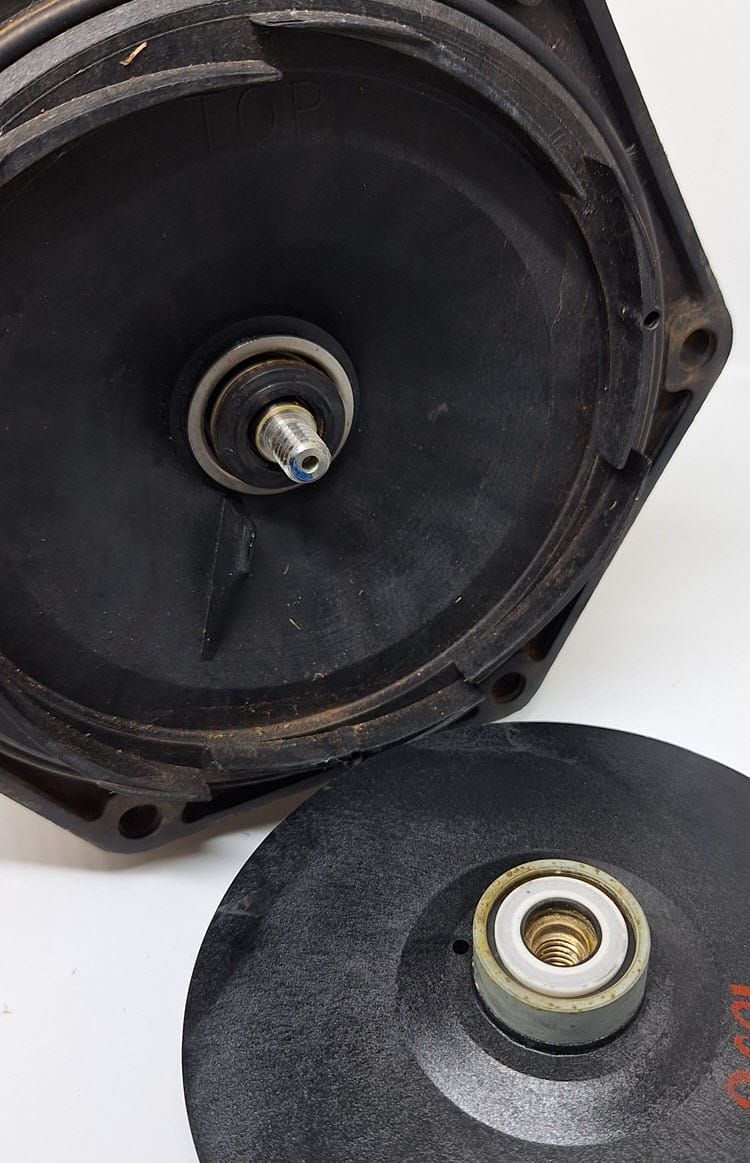
With the impellor removed you can see the 2 parts of the mechanical seal
The only problem with a pump housing, is that there is a pump shaft that goes through the wall of the housing into the inside. This is so the impellor that is attached can spin inside the housing and create the pressure. As there is a hole and a spinning shaft this creates a large problem as there has to be a gap so the shaft can spin easily but the water that is under pressure wants to escape out any outlet and this will come out this hole. The leak wastes precious water, plus flooding your pump shed and covering the motor in water which will damage it. Also when the pump is stopped, the gap will let air into the pump and so the pump will lose prime and won’t pump water again when it is restarted.
So engineers many years ago created a mechanism that seals this gap at full pressure while allowing the motor shaft to spin, the mechanical seal.
How does a mechanical seal work?
Mechanical seals are a device that allow a shaft to spin but keep the water in the pump pressurised and stop it leaking past the shaft. They generally have 2 pieces, the stationary section and the rotary section.
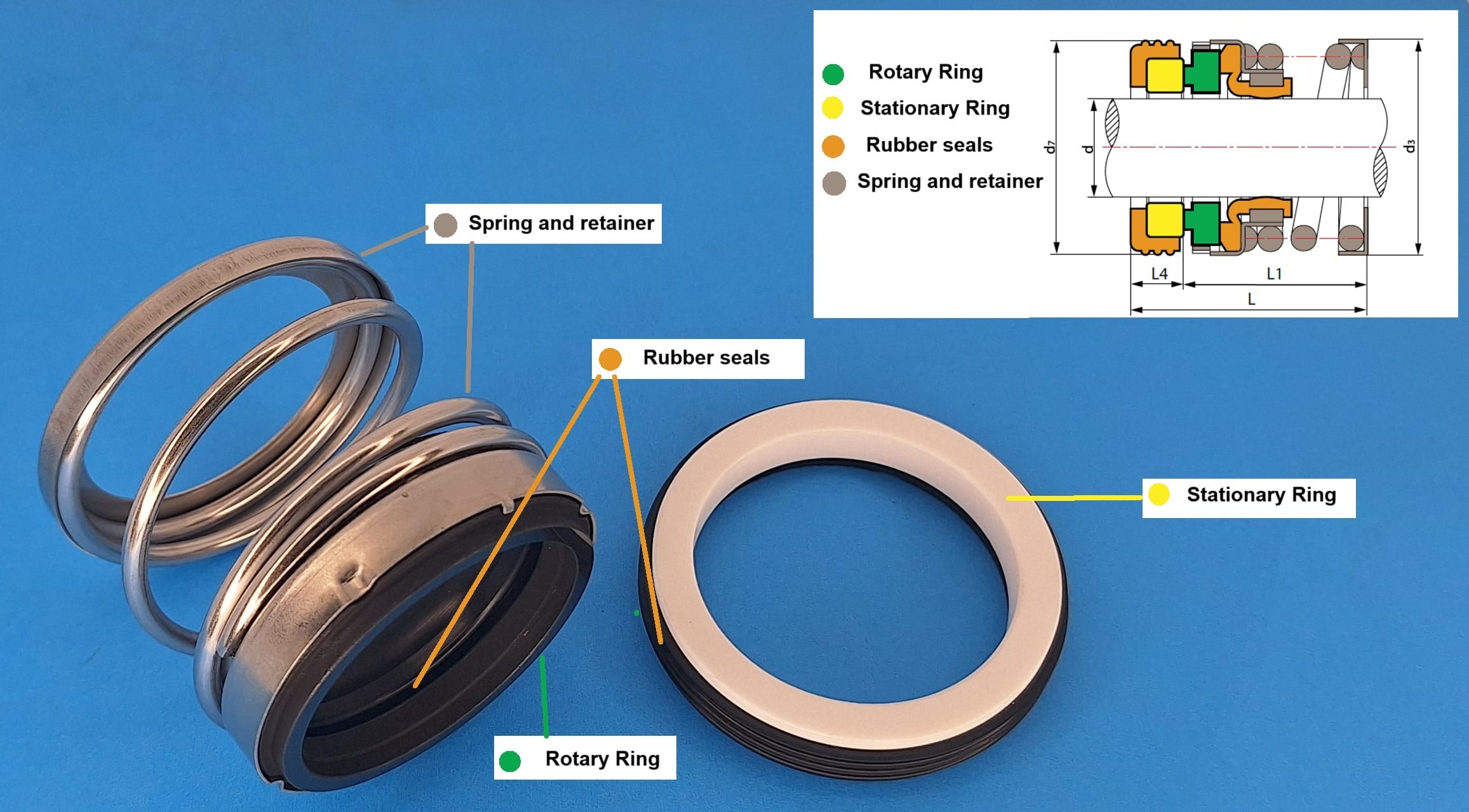
The stationary section of the seal is the part of the seal that doesn’t rotate and is set into the pump housing. This generally has 2 components, the stationary seat or face and the rubber seal that holds it in the housing and stops water going around it.
- The stationary face looks like a washer and can be made from a number of very hard but very smooth materials. In pumps they are normally made from a white ceramic or a black material, Silicon Carbide. The stationary has a hole in the middle for the shaft to pass through.
- The rubber seal is fitted to the back and outside of the stationary face and seals with the pump housing. It is usually made from an EPDM or viton rubber and is either shaped like a bowl that the seat sits in or is an O ring that fits into a grove machined into the outside of the seat.
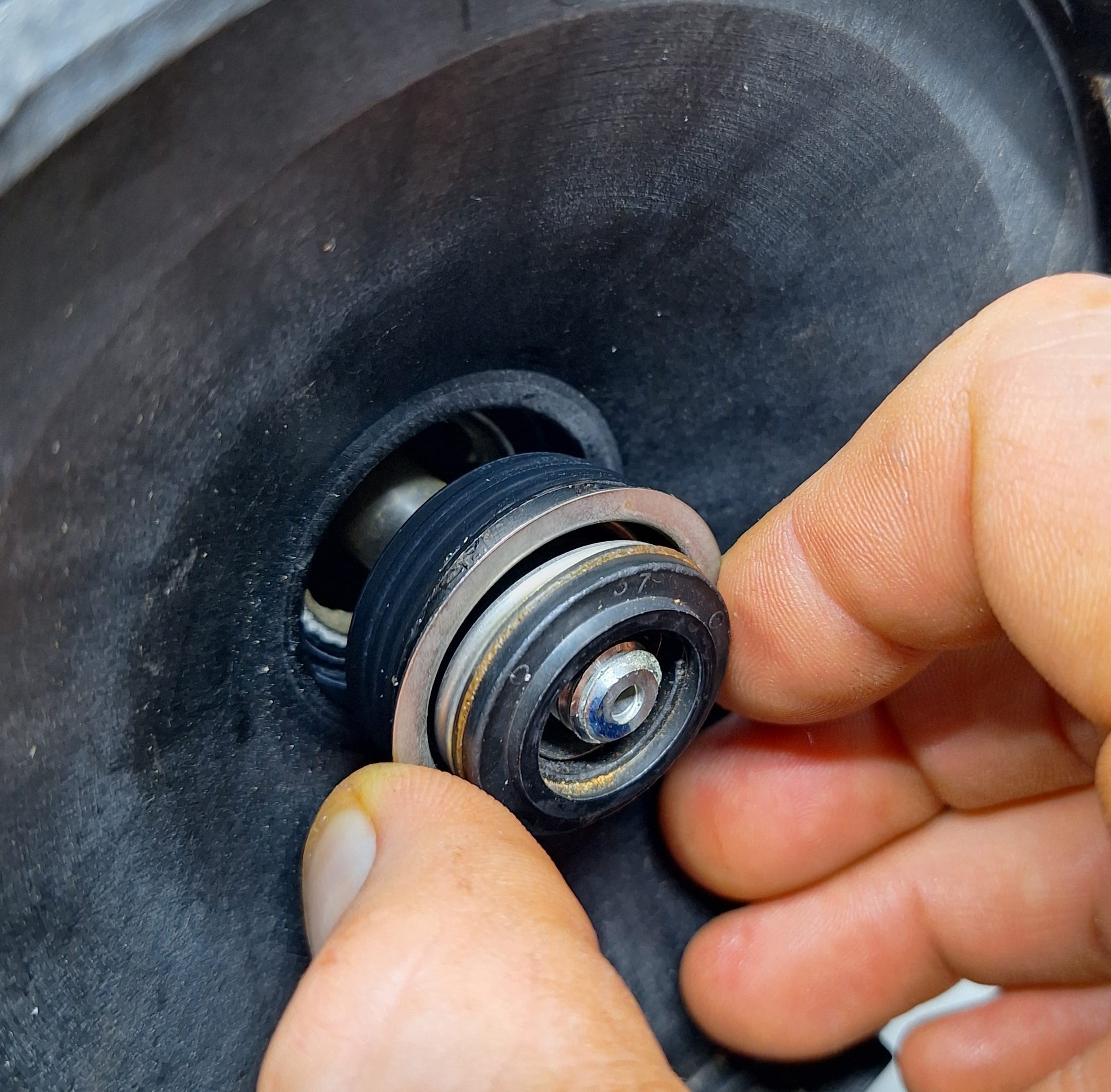
The stationary section being removed from the rear pump housing
The rotary section of the seal is the section that is attached to the pump shaft and this part spins with the shaft when the pump is running. It has 4 main components, the rotating face, the tensioning spring, a drive or locking mechanism and the bellows or seal.
- The rotating face is also shaped like a washer. It has a very flat front edge and this is pushed up against the stationary face and these are pushed together. The rotating face is usually made from either a soft material like graphite or the same Silicon Carbide as the stationary.
- The tensioning spring is as the name sounds a spring and a holder mechanism that sits behind the rotary face. When the impellor is installed and screwed down on the shaft, the impellor pushes against the spring housing which squashes the rotary face against the stationary face.
- The locking or drive mechanism can be a number or things, it is usually either a slot or notch in the inside of the mechanism or even a pin or screw. This is then matched up to a corresponding part on pump shaft that means that the rotary mechanism spins properly as it is locked to the shaft.
- The bellows or seal is a rubber membrane and sometimes and O ring on the inside of the rotary against the shaft. This stops pressurised water from going between the rotary mechanism and the impellor and then down the shaft and out of the motor.
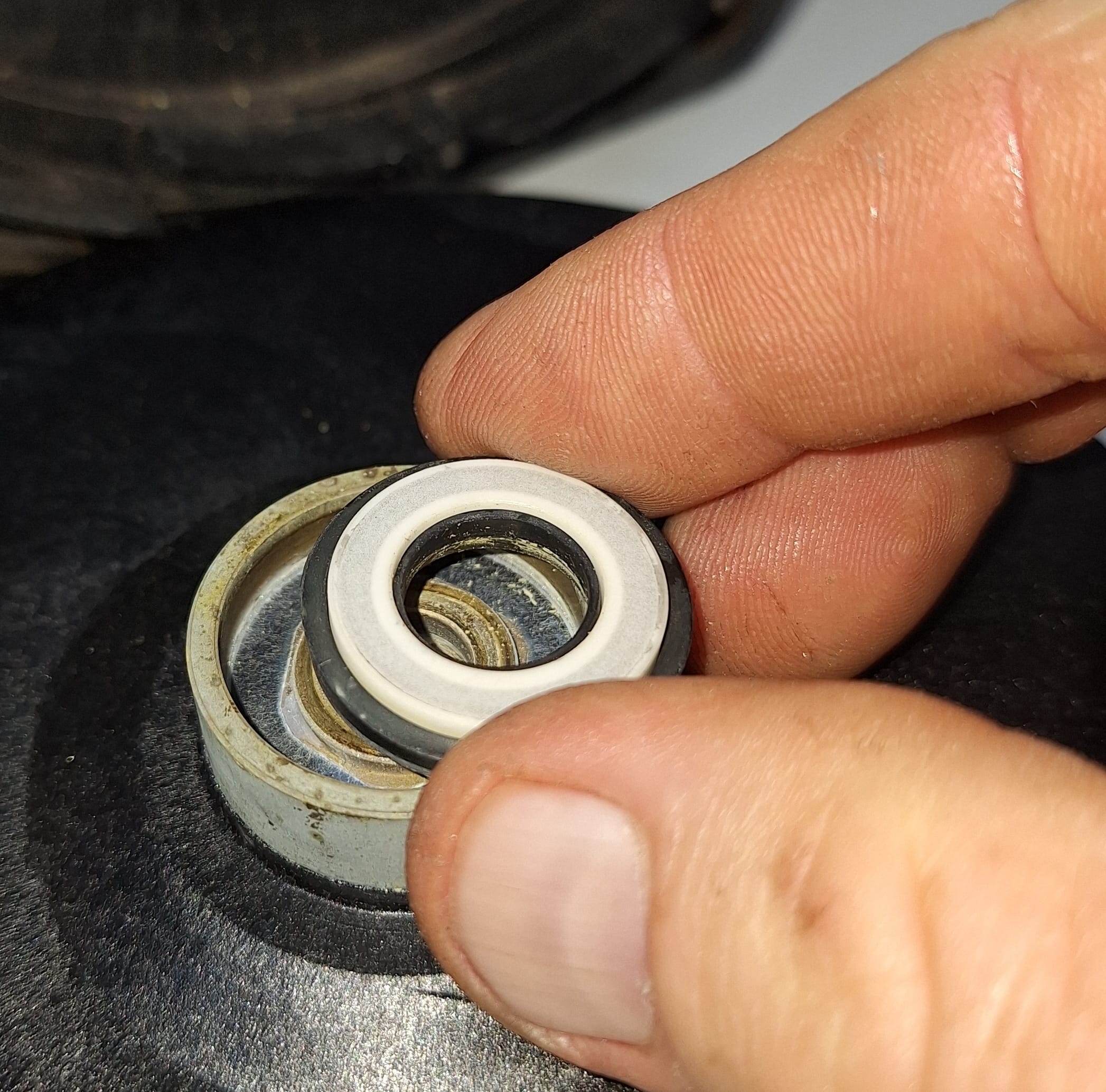
The rotary section being removed from the back of the impellor.
So what we then have when these parts are bought together is 2 flat faces on the stationary and rotary meeting and being pressed together. As they are so flat and are pushed together with a sping, then when the pump starts spinning, the shaft can spin but no water pressure can escape from inside the housing. There is sometimes a small weep of water that comes out as the 2 surfaces of the seal face are lubricated by some of the pressurised water and this stops them rapidly wearing out.
Why Are They Important?
Now as we have mentioned before, if there wasn’t a mechanical seal on your pump, then the pressure could be created but it would spray out everywhere and make a mess and cause a lot of damage. The pump also wouldn’t work properly as the correct flow and pressure won’t go up the pipe to where it is supposed to be used.
They are also important because it allows your pump to operate efficiently and reliably for many years. In the old days various materials like hemp fibre or asbestos was wrapped around the shaft between 2 plates and squeezed. The combined effect of the moisture and the squeezing made this “packing box” hold most of the water in the pump. Even so a packing box still would seep constantly as it needed water going through it to cool and lubricate the packing. This was messy, dangerous and always needed maintenance. With the invention of the mechanical seal this meant that water didn’t seep out, the materials were less dangerous and you could get years out of the seal before needing maintenance.
Do you need to fix them?
Yes you absolutely do need to fix them. The mechanical seal is probably the component that needs to be replaced most regularly in a pump, this is because the wear surfaces of the 2 faces wear out over time. This is especially true with a carbon ceramic seal as the graphite rotary is quite soft and wears down to keep its surface flat against the ceramic.
Another problems with mechanical seals is water quality. If there is mud, sand or iron build up in your water this can cause problems, this is important if your water is from a river, dam or bore water with lots of iron or manganese in it, which is common in Australia. What happens is that these particles are very hard, especially compared to the carbon rotary face and so over time water pressure will push some debris out into the seal face area. This works like sandpaper and scratches the surfaces. Then the surfaces are not able to seal against each other and begin to leak if this gets worse it can break the seal surface and water goes everywhere.
Another common fault we see in Australia is with swimming pools and pool pumps. A lot of pools in Australia are salt water pools which use an electric chlorinator to turn some of the salt into chlorine to keep the pool water safe. This high level of salt in the water (usually around 5-7g/L) is not usually a problem if the pump is running. What happens is that when the pump is stopped there is a thin film of water in the seal face, the salt in this over time forms salt crystals which work like other debris and cause damage to the carbon seat. In high salt environments or abbrasive applications we recommend using a Silicone Carbide faced seal as it is more wear resistant.
The only other time a mechanical seal is damaged is when your pump runs dry. This stops the film of lubricating water to be there and so the surfaces can rapidly wear out. Also as the dry impellor and seal starts causing friction, then the pump housing also gets hot and the rubber and plastic parts can melt or sometimes burn. If you stop it fast enough then you might only have to replace the mechanical seal but sometimes the damage is too great and the whole pump needs to be replaced.
So really the only maintenance that you need to do for your mechanical seal is to keep an eye on it. If something goes wrong, some water starts leaking out from between the pump and the motor or there is a really strange squealing sound then stop the pump and work out what is wrong. If you know how to pull the pump apart then strip it down and swap out the seal, if you don’t then get a professional to help out.
Replacing your mechanical seal.
Always remember when you have to replace the seal:
- Swap it like for like, try and match the seal type up so they look identical and have the same type of parts. Usually a pump parts supplier like Rural Pumps has the reference guides for most major pump brands so if the seal is not a common type, they can source one identical or make one from other parts.
- Always buy quality parts. Although a lot of components of seals are mass produced, make sure that you are buying from a reputable supplier, which is what Rural Pumps aims to always be.
- There is a warranty. As with all components, mechanical seals come with a warranty. They are a bit different to most other components as they are a wearing consumable part. What we cover is that the seal will work properly when you install it correctly and if the pump is used properly then the seal should work. Once a seal is past approximately 3 months then failure of the seal is no longer covered as it has started to be worn. But if a seal fails in the first week then absolutely we will cover it under warranty. We have a page on our website about our warranty policy.
- Use a grease to install it. As you are usually slipping a rubber seal into a housing or over a metal shaft, it is important that it has some lubrication so the rubber isn’t pinched and is not cut. For this we recommend a rubber O ring grease which is a silicone oil based grease. As rubber is petroleum based, then using a petroleum grease like Vaseline or bearing grease will react with the rubber and cause it to soften and swell. This will rapidly destroy the sealing ability of the rubber and cause leaks and damage. We have convenient little tubs of silicone grease in our webshop.
- If the seal is being used in dirty water or with chemicals (like in a boomspray), then sometimes the material that the seal is made from needs to be a bit better or it will get damaged. If this is the case then don’t swap like for like but contact us via email and we can recommend and supply a better seal for the job. This would typically be swapping out carbon/ceramic surfaces for Silicon Carbide which is hard and wear resistant. In the rubber most basic seals use standard EPDM rubber but this rubber can react with harsh chemicals and solvents, especially oils in insecticides and other farm chemicals. For this application we can then source Viton or other exotic rubber compounds that are designed to resist damage from harsh applications and give a good service life.
In Conclusion
So there you have it – a basic overview of mechanical seals and why they're so important in water pumps. These little components may seem small, but trust me, they play a big role in keeping your pump system up and running.
If you have any questions or queries about your mechanical seal or need help to get an unusual replacement seal for your pump, then please give us a call or send us an email and one of the Rural Pumps staff will get in touch and help solve your problem. Also check out our wide range of mechancial seals we have for sale in our webshop.